Quality Management ensures that complete visibility of quality operations including visibility of items in the quality process. Accurate costing demands that products moved through quality accurately reflect their value and are removed from appropriate WIP. Additionally, this module includes processes for supplier returns with links to Accounts Payable for automated debit processing; closing the loop on traceability of products in and out of quality within the plant. Tie together all quality functions, whether it’s scrapping end parts, rejecting raw materials or tracking first article inspections. Inspectors have queues of items to inspect with full disposition and corrective action follow-up. Plant floor employees can flag parts as nonconformant, which moves them into an inspection queue. Parts that fail inspection may be flagged for review by a material review board.
- Quality Parameters
- Quality Specification sheets and revisions
- Quality Inspection Order auto generation during purchase receipt and production receipt
- Standard Operating Procedures
- QC Equipment Master
- QC Equipment calibration schedules and calibration process
- CAPA Management
- Quality Event Managment
Quality Management Process
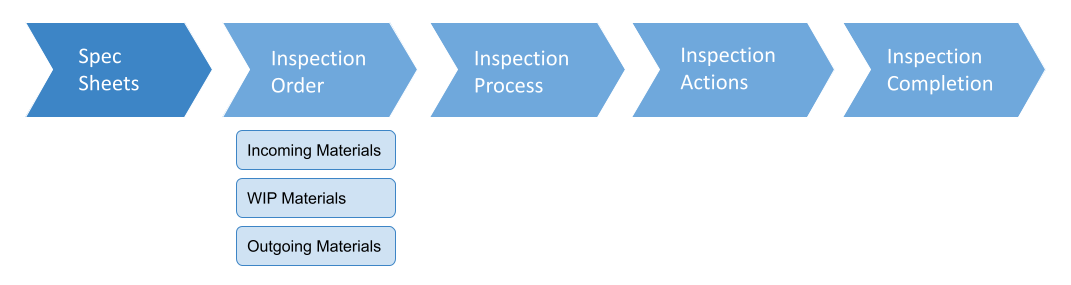
QC Checklist